Most of the infrastructure and building projects across the world use cement. Construction all around the globe demands steady supplies. Undoubtedly, the manufacture of cement enhances the economy and the environment. Now, the boring equipment in cement mills is one of the most underrated but essential machines. These boring machines make cement plant operations efficient and easy in terms of performance. Such tools are excellent at drilling nails or accurate holes and tubes for foundation works, underground walkways, field foundations, and generally in maintaining cement infrastructure. Digging machines reduce money, time, and effort by simplifying and enhancing these operations.
Modern digging machines save waste in cement manufacture and energy use, hence saving the environment. Effective drilling techniques reduce raw material waste and the use of resources, thereby reducing the carbon footprint of the industry. Cement plant digging tools grow more crucial as worldwide building grows. Their effectiveness and possibilities for sustainability make them vital to the future of cement production. New innovative equipment might be able to help companies in Boring of Marine and Cement plant machines.
Importance of Efficiency in Cement Production
Making cement manufacturing energy efficient could save money, the environment, and money. Energy is needed to cook and process raw materials. Rising consumption of energy raises costs and greenhouse gas emissions. Manufacturing can produce dust that may harm the environment if not handled appropriately. This avoids such challenges by increasing productivity. In this regard, energy-saving techniques could help cement businesses cut their expenses and minimise their harm to the environment. That is to say, smooth processes by the Insitu boring services cement industry reduce clogged-up time, increase output, and enhance global competitiveness. In this regard, the faster the production of cement, the more it will develop good habits than just earning money. This shows a company wants to balance development and environmental protection to ensure that the built environment is better for future generations.
Boring Machines and Their Role in the Industry
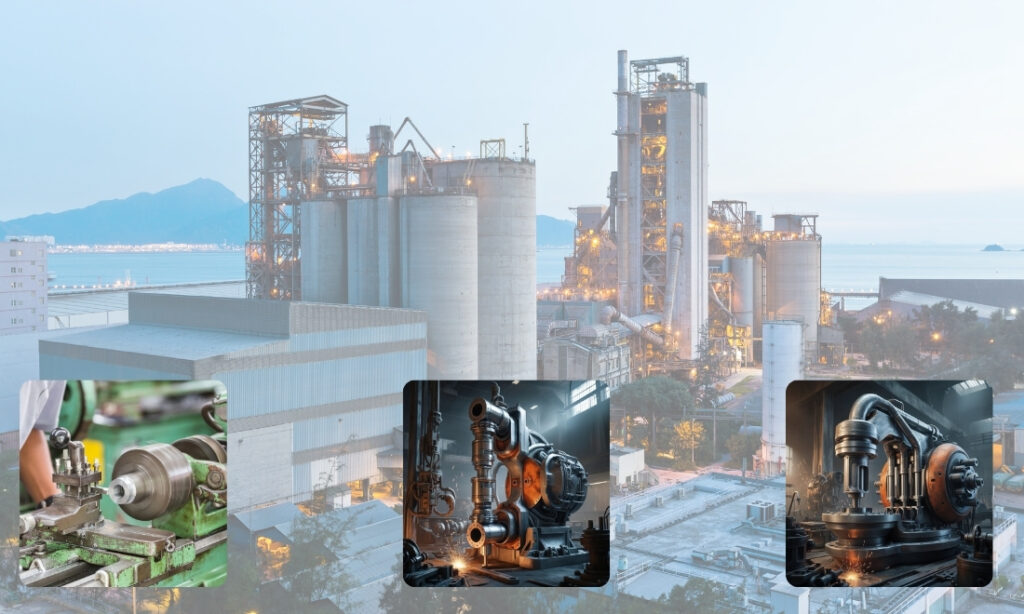
Although boring equipment has been used historically to make tunnels, nowadays, cement manufacturing depends on it for many processes. These innovative tools use rotating blades to gradually and accurately dig holes in different materials. Cement companies use them for much more than digging. They keep vital machinery moving properly. Cement plants require boiling machines, and these machines make perfect holes in machinery and structure bracing to run smoothly. Such devices wade in and speed up construction by cutting precise foundations, pipelines, and other holes that save manpower and decrease mistakes. Modern digging methods improve the safety and efficiency of a cement plant, therefore saving costs, accelerating projects, and optimising resources.
How Boring Machines Are Revolutionising Cement Plant Efficiency
Let’s delve deeper into how boring machines are transforming cement production:
The process of Boring of Marine and Cement plant machines first involves the breaking and grinding of limestone and clay into fine powder. Then these are heated to high temperatures in a spinning kiln. This produces clinker. Once it has cooled, it is crushed with gypsum and other materials into a construction material called cement.
Problems affecting efficiency: While cement manufacturing is a very vital activity, several issues face the industry and would work to its disadvantage in matters of efficiency and profitability:
Equipment wear: The circulating grinding and high temperature inside the rotary kiln wear down mill components, and the loss of precision suspends production.
Downtime for maintenance: Maintenance is necessary to keep the equipment in line and to extend its service life, but it disrupts production schedules and adds costs.
Poor Machining: Standard machining methods may fall short of the required accuracy for tools to come out right; these have adverse impacts on the quality and consistency of cement products.
Why technical progress in the cement industry is necessary: Critical and multitudes of problems have made the segment increasingly dependent on new innovative technologies. Cutting machines are gradually being introduced to improve the installation and maintenance of critical equipment. These new technologies, like automation, digital tracking, and predictive maintenance, are underway to bring about increased efficiency and reduce downtime, thereby helping cement manufacturers apply sustainable production techniques.
What are boring machines?
Definition and Meaning: Boring machines are used for the production of round holes of an accuracy class in different materials by means of spinning cutting blades. The value of these tools is very high in precise, frequent commercial contexts.
Boring tools have been in use since the time of ancient Egypt. Since then, with the addition of better control systems and CAD, they have changed considerably. These machines have made manufacturing processes more accurate and efficient.
Different industrial boring machines include line boring machines, which are applied to manufacturers and cement plants. Line-boring machines make exact holes in equipment that already exists. These tools are very helpful in setting up and maintaining machines at the cement factory. Line boring machines improve the reliability and life expectancy of the gears, thereby reducing downtime and increasing production by permitting exact angles and measurements. They are important in industries where precision is vital to achieving quality and speed due to the fact that they are versatile and very accurate.
Importance of Boring Machines in Cement Plants
Precision and accuracy: Line boring machines fabricate critical mill components to a high degree of accuracy, ensuring superior bearing seating and gear adjustment. This leads to a number of advantages in the following lines:
Gears perform better with accurate angles achieved through line boring machines, which minimise noise and wear of gears, thus improving the grinding process and extending equipment life. Cement batches do not fail as easily when milled to proper accuracy using line cutting.
Decreased Downtime and Maintenance: Time-consuming old parts used to involve disassembly, moving, and reassembling. There are a number of advantages connected with the utilisation of line digging equipment, and they include:
Role of Boring Machines in Cement Plants
Boring tools can easily fit into the maintenance of any cement plant. On-site grinding makes repairs to worn components without removing or relocating crucial parts. These boring machines are ideal for reboring grinding mill bearing seats to prolong their life at cement plants. The gearboxes are aligned with other devices for optimum output and the reduction of mechanical stress. Correct milling of shafts and other components for quality and functionality.
Boring machine operation: There are a number of companies that manufacture highly advanced cement cutting machinery. These tools have been made lightweight, precise, and strong enough for heavy materials. High-tech equipment may increase productivity, extend tool life, and improve production processes for cement companies to meet the needs of the industry.
Benefits of Using Boring Machines
Several advantages are associated with concrete factory digging equipment:
The boring machines from Insitu boring services cement industry assure the performance of the equipment and cement quality at all stages of manufacturing by facilitating accurate cutting easily. The on-site boring machines reduced equipment maintenance downtime to a great extent. Efficient cement production will save a lot. Less disassembly improves security for the workers with digging equipment. Protecting the workers from the threats of these vocations makes the work safer
Case Study 1: UltraTech Cement
Indian cement firm UltraTech Cement has upgraded its grinding mills using line cutting.
Once, UltraTech Cement had twice as much maintenance downtime. That involves on-site cutting equipment processing. Speed helped production plans stay on track and operations run smoothly. The precision cutting has improved tool performance, which led to a 10% rise in productivity. So UltraTech Cement Increased cements production to meet demand. The quality of cement becomes better when digging tools are cut uniformly and with perfection. It is due to its trustworthy nature that UltraTech Cement became popular, thereby improving the market status.
Case Study 2: Lafarge India Pvt. Ltd.:
Lafarge India Pvt. Ltd.—one of the leading Indian cement industries—moved to boring technology for its rotary kiln trunnion bearings. Here’s a comparison:
Metric | Before Boring Machines | After Boring Machines |
Downtime per Maintenance Cycle (days) | 5 | 2 |
Maintenance Cost per Cycle | $20,000 | $10,000 |
Annual Production Increase | – | 5% |
These case studies demonstrate real concrete benefits from using boring machines in cement plants: reduced downtime, lower maintenance costs, and increased production—each of which has a positive impact on the bottom line of the plant.
The Future of Boring Machines in Cement Production
Several interesting developments bring much hope to the humdrum world of cement-making tools.
Next-generation machines may be fitted with superior control systems to make them more accurate and alleviate some drudgery. Key cement plant cutting tasks will become more consistent and productive with such improvements. It’s getting easier to handle digging equipment from a distance, which means less time that maintenance personnel will have to spend in risky spots. Remote operations make workers safer and improve operations. Boring tools are increasingly connected to current data analytics and predictive maintenance systems. The link will let you schedule preventive maintenance with the aid of data concerning the performance of the machines, reducing unwarranted downtime and improving company efficiency.
Conclusion
Global cement demand dictates immediate production. Finished-at-first-sight boring equipment helps with this. Precise cutting on-site helps producers of cement to a high degree. It means reduced downtime, better equipment, and a safer environment for more efficient and cost-effective organizations. Case studies can provide examples of jobs where cost reductions can easily lead to productivity gains. Improved control systems, remote operation tools, and predictive maintenance will boost efficiency. Boring tools improve cement output, securing its future—it’s not only tunnels. Choosing Insitu boring services cement industry from MPA Power Project boring options can be quite effective in this matter.
No Comments